Article from the Australian Cottongrower Magazine. Download PDF
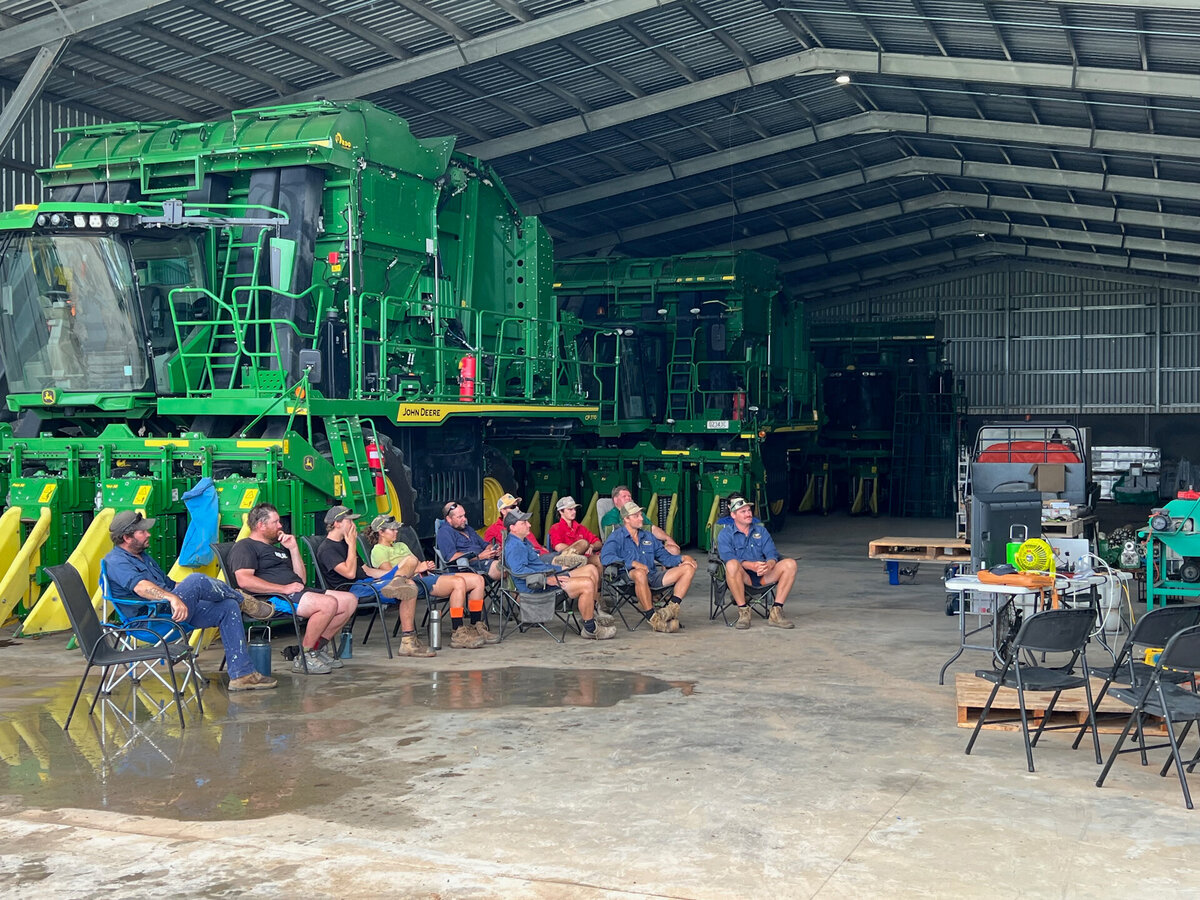
Cotton Australia has secured Queensland Government funding to deliver a series of task-specific workshops, aimed at providing valuable training throughout the state.
The announcement is part of the Queensland Governments’ Micro-credential Program, which will upskill Queensland’s existing workers or job seekers by enabling the provision of training in specific skills.
As part of that program a total of $3.4 million was provided for 17 projects to upskill more than 7500 Queenslanders.
Paul Sloman, Cotton Australia’s workforce policy officer said the funding will provide workshops to solve one of the most important workplace skills shortages for cotton growers.
“Cotton pickers are technologically advanced pieces of machinery, and they are worth in excess of $1.5 million each so anyone who wants to drive one to help a grower pick their crop, has to know what they are doing.”
Under the funding package, Real Skills Ag Training will deliver 10 workshops across Queensland cotton producing regions commencing in January/February 2024, allowing 70 staff from cotton growing businesses to be upskilled in cotton picker operations. At this stage, Queensland workshops are planned for:
- Emerald;
- Theodore;
- Darling Downs x 3;
- St George;
- Dirranbandi;
- Talwood;
- Goondiwindi; and,
- Mungindi.
The workshops will see a heavy focus on safety, problemsolving and general operation of the current model John Deere round bale cotton pickers. Participants will receive ongoing access to course content, videos and mentoring.
Troy Smith will be delivering the training courses and will be seeking hosts in Central Queensland, the Balonne, Border Rivers and the Downs. The training day is most valuable delivered in a shed, on farm right next to a picker or two.
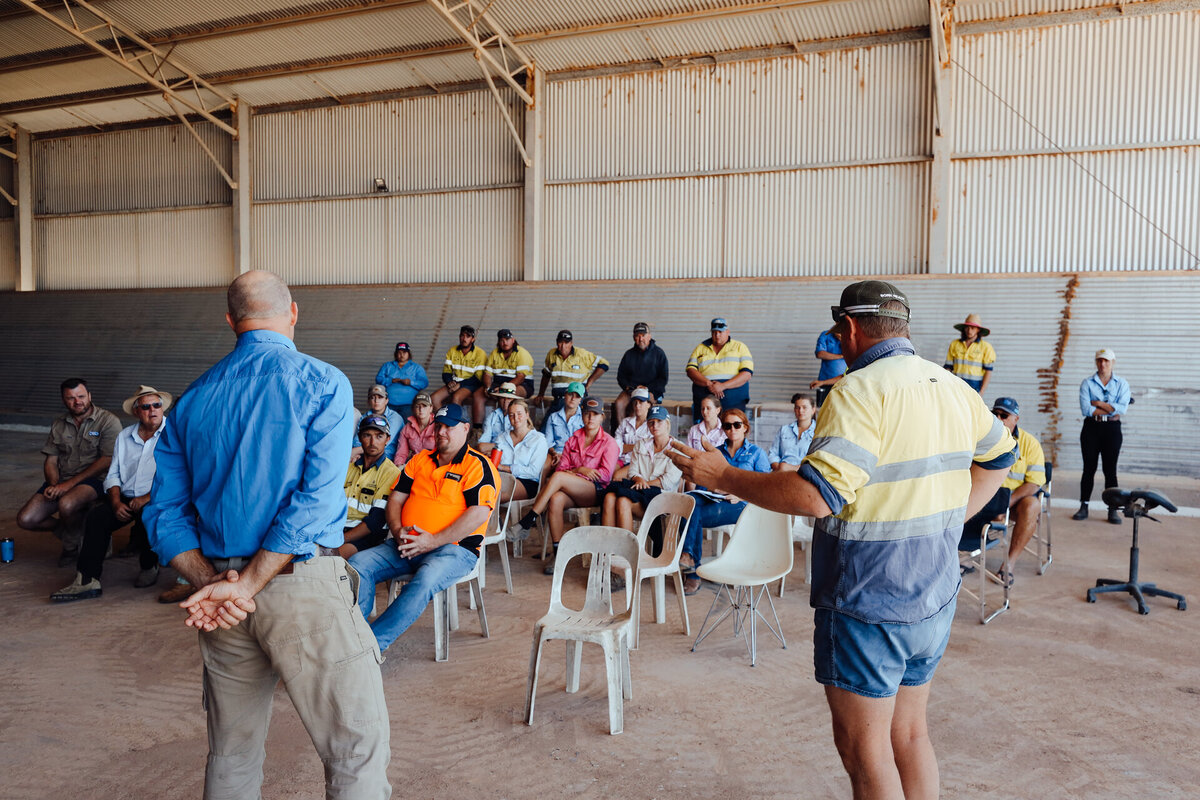
Courses in NSW
The situation in NSW is unchanged from last year, where it is not subsidised but the courses will still be available and Troy is confident in the value proposition that this training offers.
Cotton Australia will be lobbying the NSW government to support micro-credential programs in the future.
Last year Troy delivered 26 training days from Emerald in the north to the Murrumbidgee in the south, with seven in Queensland and 19 in NSW to over 200 attendees.
“I mainly focused on the new John Deere CP770 with the course,” says Troy, “and it was designed with new or fairly new operators in mind. Last season showed me that there is still significant demand for training operators of the older machines that won’t go away anytime soon, and it also showed me that even quite experienced operators and owners who attended gained something.
“They are very complex machines and to profit from sending people to the course, we need to only save one hour of downtime over the entire season.”
The course is also a blueprint for operator excellence on any machine that participants go on to operate. There is also a safety component covering major picker related issues like powerline contact, working at heights, manual handling of the heavy rolls of module wrap, protective equipment, safety stops and locks, entanglement risk and more.
“Doing a job safely is doing a job right,” says Troy. “We rightly expect high levels of productivity from these machines, but safety and productivity can exist together.
“Many owners saw the training days as an opportunity for a team culture day, and brought along other members of the team, not just the picker drivers. We’d have a nice BBQ lunch and it was really valuable to have the owners and managers adding to the discussions around safety, procedures and ultimately productivity. Picking really is a team effort and it was really pleasing to see this team development happening on many farms.”
The courses will start in January/February in central Queensland and finish when the last machines enter the paddock in the Murrumbidgee, hopefully by late April.
The course is video based, shot in real field conditions over multiple seasons. There is a benefit to being able to show people how things need to be done. This saves significant time in those first few days of picking, paving the way for a smoother, quicker and safer harvest.
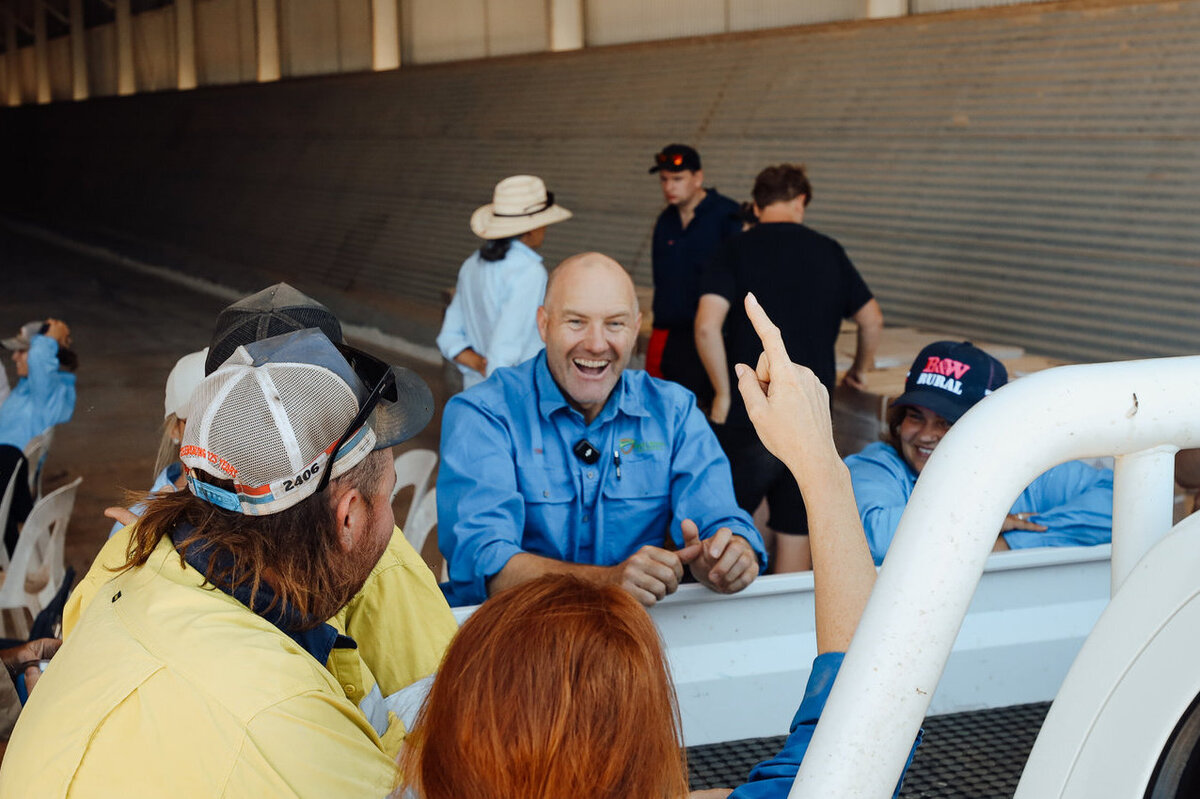
Troy Smith Story
Troy grew up around Garah/Mungindi, and started module building and sweeping the roof and cleaning heads on 9910 two row pickers after school and in the Easter holidays.
As he got older and started managing harvests, he found picking time incredibly stressful: training new operators, trying to keep everyone safe, looking after the machinery and doing all he could to get that crop off before it rained.
The biggest frustration was that there was no opportunity to train operators until the machines entered the field, and if the crop was ready, it was difficult to accept being slow for a day or two while the team got trained. But trying to get productive too quickly causes more issues than taking the time and doing it properly.
In 2005 Troy had enough of farm management and moved to the Sunshine Coast with his young family. Then, at Easter 2021, his brother Glen asked him to come back and drive a picker and help in the gin since he was facing Covid based workforce issues on top of some crippling drought years.
“Glen just needed an extra set of eyes with machinery experience to help train new operators on Moonbuggies, spear loaders, bale loaders etc. I was a bit intimidated at first, having never done those exact jobs before but it really showed how most machinery operation is similar.
“We’ve got to do it safely, we’ve got to take the time to train operators and allow them to work slowly for a small period while their skill and muscle memory develops and then we expect solid productivity, all the while looking after the machine properly. The recipe works for anything, if communicated properly.”
It was Troy’s first experience on a round bale picker and while he was operating that 7760, there was also second one working with a young operator on it.
“He was doing pretty well, but could use some polish,” says Troy. “Head blocks were taking a long time to clear, turns weren’t as slick as they could be, these little things didn’t seem like much but by the end of the season my machine had made 20 per cent more modules – that’s five machines doing the work of six. A few lightbulbs went off for me; that there is a real value proposition to improving the skills of even “trained” operators; that I really enjoyed
training people and was good at it; and that while plenty of people had my skills, most of them were simply too damn busy to properly pass them on.”
Once picking was finished, he spent a few months working at the gin and made some introductory training videos for the gin machinery. Video editing was a new challenge and he was amazed at the time it took to actually create a 10 minute video.
“A video can’t be your entire training, but it can do some of the repetitive messaging for a busy manager, and makes sure that you don’t leave something out when making it up as you go along. And it can provide a significant increase in productivity for an operator.
The next year, Troy made a video based course for the newer John Deere machines. It covered morning service, prestart, walk around, warm up, door blocks, broken modules, what a portion of wrap looks like, how to perform a manual wrap and eject, what to watch for on the cameras, how to set the camera triggers and screens, how to do excellent turns, how to set the doffers and moisture columns, what dirty spindles and wrapped spindles look like, a good blowdown and much more.
“All along safety was at the forefront of my mind,” says Troy. “I’ve had colleagues killed and badly injured at work and a cotton picker can be a dangerous machine. Safety is about highlighting the major risks but more so it’s about being a safe person or becoming a safe person. Safety is an integral part of technical skills training, it’s not a stand-alone topic.”
Rule #1 of Real Skills Ag Training is ‘Survive the Day.’
Rule #2, is ‘Start slower to finish sooner.’ It is important to take the time during the first day or two of picking to settle the machine in and allow the operator to practice things like turns really slowly at first, and allow those skills to develop without pushing too hard.
Then we get to Rule #3, Get Uppa. The plan is to pick cotton, and heaps of it, and that involves mastery level operation, turns, speed management, height management, moisture management and in-season maintenance including that all important blowdown.
Learn more about our Safety Training
All news articles News